1510 W. Drake Drive, Tempe, Arizona USA 85283
8 Reasons You Should Buy VHA Main Rotor Blades Now
SHARE THIS POST:
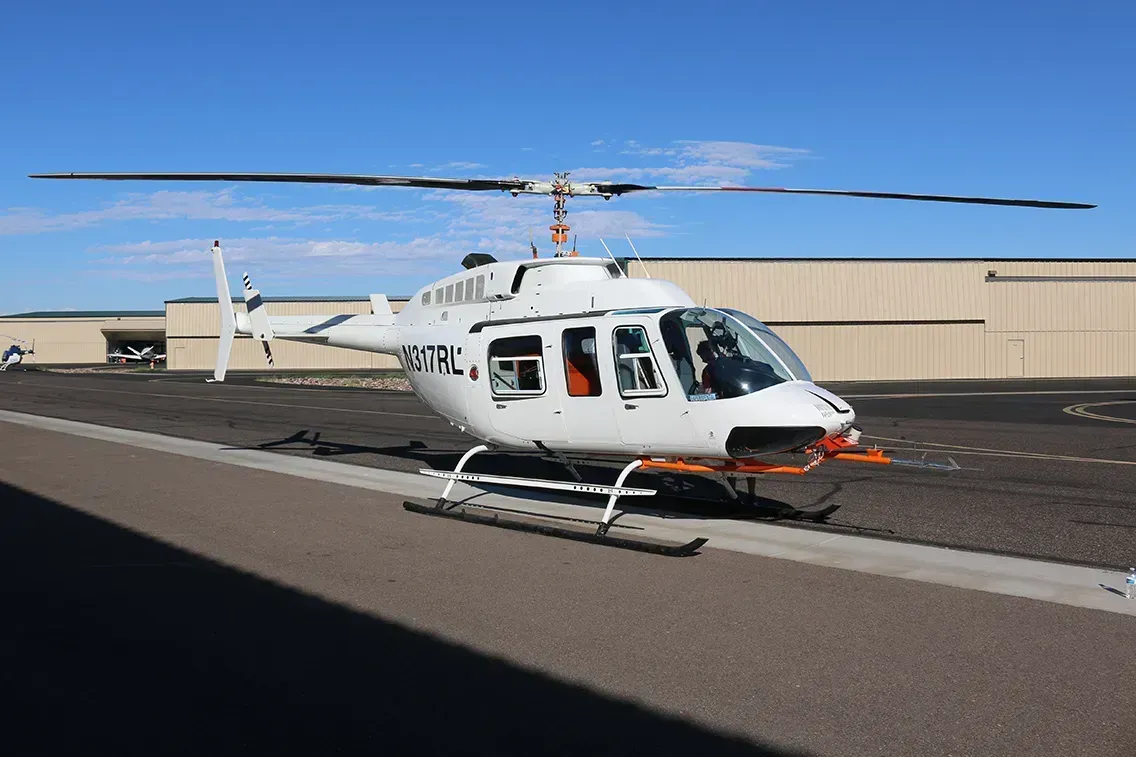
For 206L LongRanger operators flying P/N 20633000-101 serial numbers A007-A009 or A012-A104, we would like to remind you that these blades are subject to AD 2022-22-08, which requires recurring tap inspections every 400 flight hours or 2,400 engine starts, whichever comes first. You can learn more about the tap test requirements and procedure in our video . These blades are likely to develop a delamination in the area of the weight pocket on the lower surface of the blade. The AD further requires removing the blades from service if the delamination reaches 6 inches in length. However, extensive company testing indicates that all blades will likely achieve their full retirement life before that occurs. So long as the delamination is monitored and does not exceed the permitted length, the blades are entirely safe to fly with no adverse effects on aircraft behavior or performance. Operators are required to report their findings at every inspection interval to VHA for tracking using the form on the last page of Service Bulletin 33000-4 . Completed forms should be emailed to info@vanhornaviation.com . Providing this data helps to ensure all operators of these blades remain safe. All of the identified blades are likely to have delaminations, so if none are detected please contact us for assistance. In addition, this AD is considered an interim action and once sufficient data is gathered it may be updated to reduce the required frequency of inspection. Refer to AD 2022-22-08 and SB 33000-4 for further information.